Continuous Improvement Processes: Choosing The Right One For Your Business
By Julian Lewis • May 15, 2024

Introduction: The Importance of Continuous Improvement Processes
Why Embrace Continuous Improvement?
In today's fast-paced business environment, the ability to adapt and improve continuously isn't just a benefit—it's a necessity. Continuous improvement not only streamlines processes but also fosters a culture of proactive problem-solving and innovation. By embracing this approach, organizations can not only improve efficiency and reduce costs but also enhance employee engagement and customer satisfaction, creating a sustainable competitive advantage.
Understanding the Scope and Impact
The scope of continuous process improvement extends beyond mere incremental adjustments; it encompasses a fundamental transformation in how a company operates. From the factory floor to the executive suite, every aspect of the organization is subject to scrutiny and potential enhancement. This journey involves not just identifying and eliminating waste but also strategically enhancing processes to exceed customer expectations continually. The impact of such comprehensive improvement efforts is profound, leading to significant breakthrough improvements that can redefine the market standards.
By integrating methodologies such as Lean management, Six Sigma, and the Agile methodology, businesses can achieve a holistic improvement that touches every part of the process flow, from increased efficiency and quality to innovation and market adaptability. These methods provide the tools and frameworks necessary to undertake this critical journey effectively, making continuous improvement not just an ongoing effort but a foundational business strategy.
Engaging in this continuous improvement journey allows organizations to adapt quickly to new challenges and opportunities, turning potential threats into advantageous innovations. As the business landscape evolves, the ability to continuously improve will distinguish industry leaders from the rest.
Join our Newsletter
Transform your career with our personal growth insights. Get one valuable tip right in your inbox every Saturday morning.
What is Continuous Process Improvement?
Definition and Core Concepts
Continuous Process Improvement (CPI) is a strategic approach focused on improving the efficiency and effectiveness of an organization's processes. At its core, CPI involves identifying, analyzing, and improving existing business processes to meet new goals and objectives, typically aimed at enhancing productivity, reducing costs, and improving overall process quality. This method relies on a systematic evaluation of an organization's workflows, seeking opportunities for improvement through incremental changes—small but significant modifications that cumulatively lead to substantial performance enhancements.
The Evolution of Continuous Improvement Methodologies
The concept of CPI has evolved significantly over the years, adapting to the changing needs of businesses and incorporating a variety of philosophies and tools. Initially rooted in manufacturing, as demonstrated by the Toyota Production System and its emphasis on eliminating waste, CPI has transcended its industrial origins to become fundamental in various sectors, including services and technology. Methodologies such as Total Quality Management (TQM), Lean practices, and Six Sigma have further refined and expanded the approach, each contributing frameworks that emphasize waste reduction, quality improvement, and customer satisfaction. More recently, the integration of technology and data analytics has given rise to Agile methodologies which prioritize adaptability and customer-centricity, proving that continuous improvement is not only ongoing but also ever-evolving to meet the demands of a dynamic business environment.
Assessing Business Needs and Goals
Aligning Improvement Processes with Business Objectives
To effectively implement continuous process improvement, it is crucial to align these initiatives with broader business objectives. This alignment ensures that each enhancement directly contributes to the overarching goals of the organization, whether it's increasing efficiency, reducing costs, or enhancing customer satisfaction. By integrating improvement processes with business strategies, companies can create a cohesive framework that not only supports current operational needs but also drives future growth and competitiveness.
Identifying Key Performance Indicators (KPIs)
Key Performance Indicators (KPIs) are essential metrics used to measure the effectiveness of continuous improvement efforts. Selecting the right KPIs involves understanding the critical aspects of process flow and improvement strategies that directly impact business outcomes. These indicators should provide clear benchmarks for success and offer insights into areas where processes can be streamlined to better meet customer expectations. Effective KPIs help organizations identify opportunities for significant enhancements, ensuring that improvement efforts are both targeted and measurable.
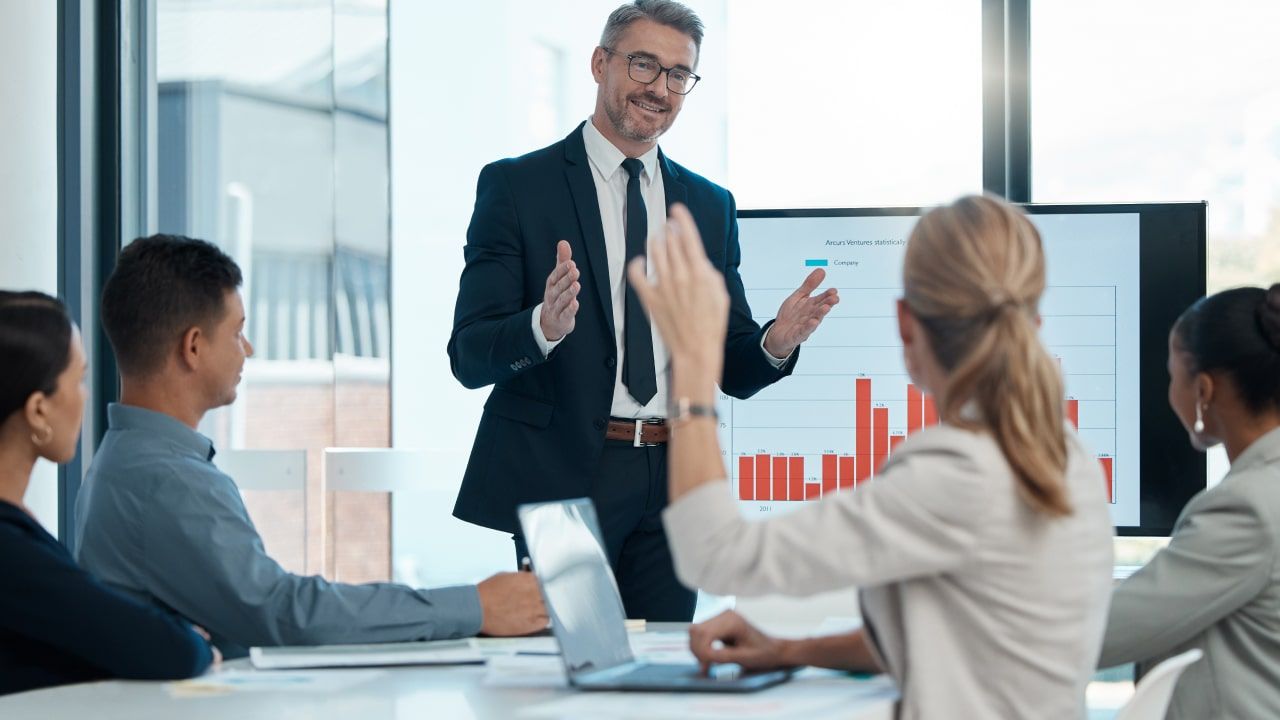
Determine Your Key Processes
Mapping Out Core Business Processes
To effectively optimize operations, it is crucial to perform value stream mapping—a visual tool used to analyze and design the flow of materials and information required to bring a product or service to a consumer. This comprehensive mapping helps clarify the entire process and pinpoints inefficiencies and non-value added activities. By thoroughly understanding your current processes, your organization can streamline operations to eliminate waste, enhance process flow, and significantly improve overall efficiency.
Identifying Areas for Improvement
Once the core business processes are clearly mapped out, the next step involves identifying bottlenecks and areas that are ripe for improvement. This critical evaluation looks for opportunities within the process that can be enhanced to reduce costs, increase efficiency, and improve quality. Streamlining these processes is not just about reducing the time or cost it takes to produce a good or service but also about enhancing the overall agility and responsiveness of the organization to meet customer demands and exceed their expectations more effectively.
What to Look For When Choosing a Continuous Process Improvement Tool?
Essential Features of Effective Tools
When selecting a continuous improvement tool, it is crucial to evaluate features that align with your business's specific needs. Effective tools should facilitate the streamlining of processes, provide clear data visualization like value stream mapping, and support root cause analysis. They must integrate seamlessly with existing systems and be adaptable to various methodologies, whether it’s Lean, Six Sigma, or Total Quality Management. The ability to analyze data quickly and accurately, identify bottlenecks, and track improvements over time is essential for any tool aimed at fostering ongoing improvement efforts.
Comparing Popular Tools and Methodologies
Several widely-used methodologies offer structured approaches to process improvement. Lean methodology focuses on waste reduction and efficiency, while Six Sigma emphasizes defect reduction and precision. Total Quality Management (TQM) integrates the entire organization in improvement efforts, from the ground up. Comparing these tools involves looking at their suitability for your specific process flow, the scalability they offer, and how well they can be tailored to meet customer expectations and achieve incremental improvements. Each tool has its strengths and is best suited to different types of process challenges. Selecting the right one can dramatically improve quality, reduce costs, and enhance customer satisfaction.
Overview of Continuous Improvement Tools and Methodologies
Lean Manufacturing
Lean Manufacturing is a methodology derived from Toyota's production system, which emphasizes waste reduction across all areas of production without sacrificing productivity. The focus is on streamlining processes, eliminating non-value-added activities, and improving product quality. Key practices include value stream mapping and the use of Kanban boards to optimize workflow. Lean’s primary goal is to enhance efficiency, reduce waste, and incrementally improve processes through continuous and breakthrough improvements.
Six Sigma
Developed in the 1980s, Six Sigma is a data-driven approach focused on reducing defects and variability in processes to improve overall output quality. It utilizes two key methodologies: DMAIC (Define, Measure, Analyze, Improve, Control) for existing processes, and DMADV (Define, Measure, Analyze, Design, Verify) for new processes. Six Sigma tools are used to precisely identify root causes of defects and streamline quality control, providing a scientific method to quality management that exceeds customer expectations through rigorous data analysis and process improvement.
Total Quality Management (TQM)
Total Quality Management (TQM) involves continuous improvement of all organizational processes, leading to high customer satisfaction levels. This holistic approach encourages a collaborative and participatory work environment where every employee is engaged and committed to maintaining high standards of workmanship. TQM’s strategies involve integrating all functions and processes related to quality across the company, ensuring that quality improvement is continual and improvements are sustained over the long term.
The Kanban Method
The Kanban Method is a visual system for managing work as it moves through a process. Kanban visualizes both the process (the workflow) and the actual work passing through that process. The goal is to identify potential bottlenecks in your process and fix them so work can flow through it cost-effectively at an optimal speed or throughput. This method is particularly effective in environments where work requirements are constantly changing, such as software development and service tasks.
Agile Methodology
Agile Methodology is primarily used in software development but has been successfully adapted to other fields. It emphasizes flexible responses to change, incremental, iterative work sequences known as sprints, and fosters a team environment where everyone shares responsibility for customer satisfaction. Agile’s adaptability makes it suitable for projects where requirements evolve frequently, and a fast turnaround is critical. The methodology promotes continuous iteration of development and testing throughout the project life cycle, increasing employee engagement and ensuring that the end product aligns closely with customer needs.
Each of these methodologies offers unique benefits and can be tailored to specific organizational needs, depending on the type of processes and outcomes desired. By leveraging these tools, organizations can significantly improve their operational efficiency and increase the quality of their outputs, aligning closely with the goals of continuous process improvement.
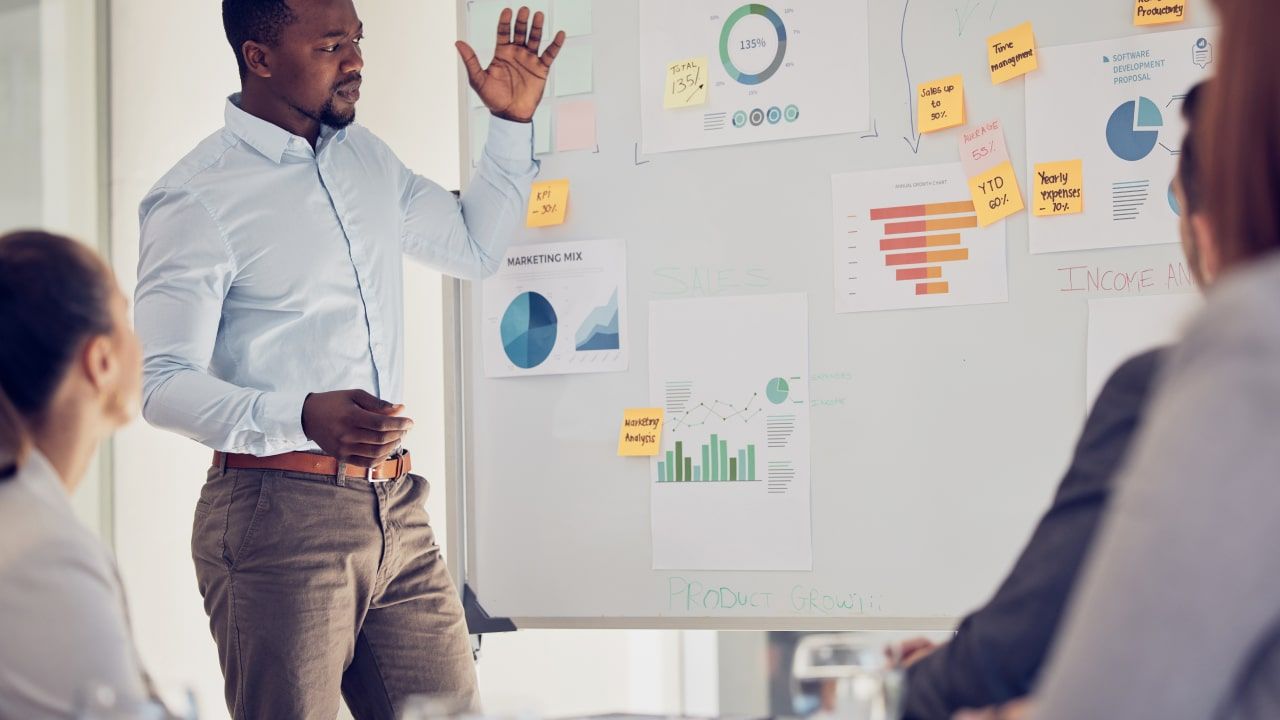
The Four Steps of Continuous Process Improvement
Plan: Identify the Root Cause of Problems
The Plan step in the PDCA (Plan-Do-Check-Act) cycle involves a thorough analysis to identify the root causes of deficiencies within existing processes. Utilizing tools like root cause analysis or the fishbone diagram ensures that the underlying problems are discovered and not just the symptoms. This stage sets the foundation for effective process improvements by accurately pinpointing issues that need addressing, preparing the ground for developing actionable and targeted solutions.
Do: Develop Improvement Plans and Solutions
Once the root causes are identified, the Do phase focuses on developing and implementing solutions to these problems. This step involves detailed planning and the execution of improvement strategies that are designed to eliminate inefficiencies and enhance process quality. Solutions are typically tested on a small scale during this phase, allowing for adjustments and refinements before full-scale implementation, ensuring the solution is viable across the entire process.
Check: Verifying the Effectiveness
The Check step is critical as it involves evaluating the effectiveness of the implemented solutions against predefined metrics or goals set during the Plan phase. This evaluation often involves measuring process performance to ensure that the changes have led to the desired improvements in efficiency, quality, and cost-effectiveness. Tools like statistical process control or real-time data monitoring are used to assess outcomes and identify any gaps in the improvement efforts.
Act: Implementing the Solution
In the final Act step, successful solutions are fully integrated into the process, and standard operating procedures are updated to reflect the new methods. This phase is about institutionalizing the improvements and ensuring that they are sustained over time. The Act step may also involve scaling the solution across the organization if the improvements have proven effective during the Check phase. Continuous monitoring and regular revisits of the process ensure ongoing optimization and facilitate a culture of continuous improvement.
This PDCA cycle, also known as the Deming Cycle or Shewhart Cycle, is a proven framework that guides teams through a logical sequence of steps for effective process improvement. It not only supports solving existing problems but also institutionalizes a way of thinking within the organization, promoting a proactive approach to identifying and addressing future challenges.
Join our Newsletter
Transform your career with our personal growth insights. Get one valuable tip right in your inbox every Saturday morning.
Creating a Culture for Continuous Improvement
The Role of Leadership and Management
Leadership and management play a pivotal role in fostering a culture of continuous improvement within an organization. By actively promoting and participating in improvement initiatives, leaders set the tone for an environment where continuous improvement becomes a part of the organizational DNA. This involves not only providing the necessary resources and training but also by being actively involved in improvement projects, recognizing and celebrating successes, and encouraging a mindset of ongoing improvement among all employees.
Improved Employee Engagement and Relationships
Creating a culture of continuous improvement significantly impacts employee engagement and workplace relationships. When employees are actively involved in identifying improvement opportunities and developing solutions, they feel valued and empowered. This involvement not only increases their engagement but also fosters a sense of ownership and accountability towards their work and the organization's goals. Furthermore, working collaboratively on improvement initiatives can strengthen team relationships, improving communication and collaboration across departments. This collaborative environment encourages sharing ideas freely, which is critical for sustaining continuous improvement efforts and promoting a positive work environment where everyone is committed to excellence.
Implementing Changes and Evaluating Results
Straightforward Implementation
The implementation of changes in the process of continuous improvement should be straightforward and clear. Simplifying the implementation phase ensures that all stakeholders understand their roles and the expected outcomes. This approach minimizes resistance and facilitates smoother transitions, allowing for the quick realization of benefits. Effective communication and training are essential during this phase to ensure everyone is on board and fully understands the necessary changes and how they contribute to the organization's objectives.
Collect and Analyze Data
Data collection and analysis are crucial steps in both implementing changes and evaluating their effectiveness. By gathering relevant data before and after implementing changes, organizations can obtain a clear, objective view of the impact. This data serves as the basis for analysis, helping to identify trends, measure progress against key performance indicators (KPIs), and pinpoint areas for further improvement. The use of analytical tools and techniques can aid in this process, providing insights that guide decision-making and improvement strategies.
Evaluating the Results
Evaluating the results of implemented changes is a critical step in the continuous improvement process. This evaluation involves comparing the outcomes to the objectives set during the planning phase to determine if the changes have successfully addressed the root causes of problems and improved process performance. It's also an opportunity to reflect on what worked well and what could be improved in future cycles. Regular evaluation not only ensures that the improvements are sustained but also fosters a culture of accountability and continuous learning, driving further improvement efforts and contributing to the ongoing success of the organization.
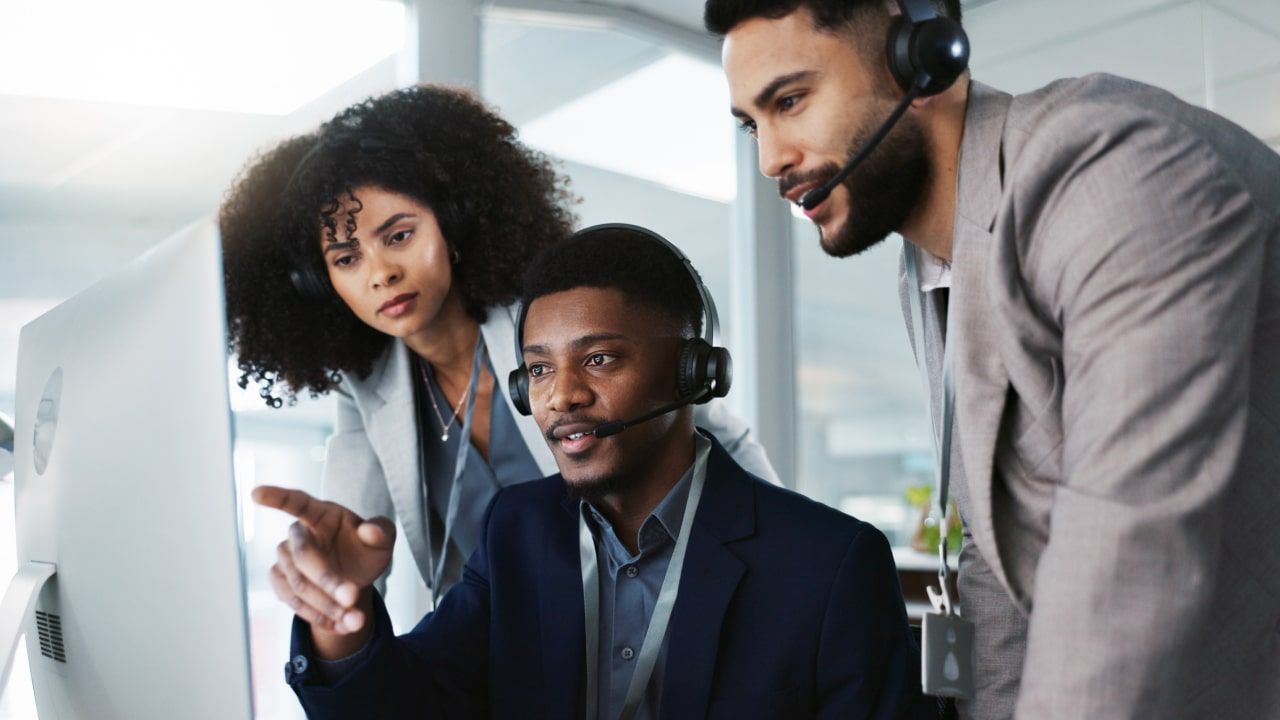
Benefits of Embracing Continuous Improvement
Increased Efficiency and Productivity
Embracing continuous improvement methodologies such as Lean, Six Sigma, and Agile can significantly increase operational efficiency and productivity within an organization. These methods streamline processes by eliminating waste and reducing unnecessary steps, which not only speeds up production but also enhances the quality of the output. Increased efficiency often leads to better resource management, allowing employees to focus on more value-added activities, thus fostering a more productive work environment.
Reduced Costs and Cycle Time
One of the most tangible benefits of continuous improvement is the reduction in costs and cycle times. By optimizing processes and eliminating inefficiencies, organizations can drastically lower their operational expenses. Improvements such as reducing material waste, optimizing energy usage, and improving labor efficiency directly translate into cost savings. Additionally, shorter cycle times mean faster turnaround, which can be a critical competitive advantage in fast-paced industries.
Improved Quality and Customer Satisfaction
Continuous improvement efforts are fundamentally aimed at enhancing product or service quality. Methods like Total Quality Management and Six Sigma focus on minimizing defects and inconsistencies, which leads to higher quality outcomes that exceed customer expectations. Improved quality naturally boosts customer satisfaction, as clients receive products and services that meet their needs and preferences more effectively. This not only helps in retaining customers but also in attracting new ones through positive word-of-mouth and higher customer loyalty.
Increased Innovation and Competitive Advantage
Regularly applying continuous improvement processes fosters an environment of creativity and innovation. Employees are encouraged to think critically about their workflows and suggest improvements, which can lead to significant breakthroughs in products, services, and internal processes. This continuous cycle of innovation enhances the organization's adaptability and responsiveness to market changes, providing a substantial competitive edge. Organizations that consistently innovate are better positioned to lead the market, adapt to new challenges, and meet the evolving needs of their customers.
Through these benefits, continuous improvement proves to be not just a set of tools or methodologies, but a strategic approach that can transform an organization. It enables businesses to thrive in competitive environments by continuously adapting and improving every aspect of their operations.
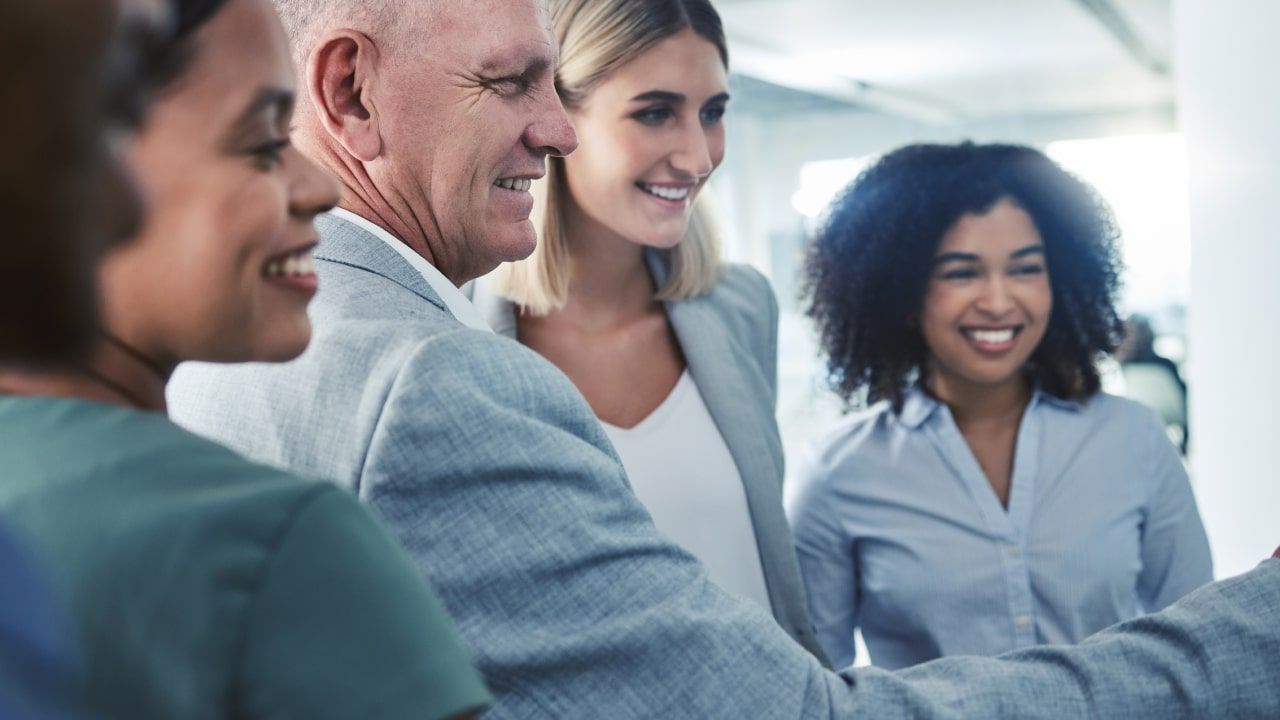
Conclusion: Sustaining Improvement and Fostering Innovation
Recap of Continuous Improvement Importance
The journey of continuous improvement is crucial not only for maintaining competitiveness but also for fostering an environment where innovation thrives. This journey has been detailed through a systematic exploration of various methodologies that support ongoing enhancements—from Lean practices to Six Sigma and beyond. These processes help businesses adapt quickly, drive efficiency, and sustain incremental improvements that cumulatively transform organizational performance.
Future Trends in Continuous Improvement Processes
Looking ahead, continuous improvement processes will increasingly incorporate advanced technologies such as AI and machine learning to predict trends and automate improvements. This integration will facilitate deeper insights and faster adaptation, ultimately enhancing the precision of improvements. Furthermore, as global competition intensifies, the ability to rapidly implement and scale effective solutions across geographical and cultural boundaries will become a key differentiator. Continuous improvement efforts will be more data-driven, tailored, and integrated, ensuring that organizations not only survive but excel in an ever-evolving business landscape.
Read more about: Professional Development, Productivity, Leadership
About Julian Lewis
Julian Lewis is a driven and accomplished professional with a passion for driving positive change in the business world. He is the co-founder and COO at Zella Life.
His own experience as a professional of color in a Fortune 500 company led him to discover the limitations for advancement that many professionals like himself face. Determined to reach his full potential, Julian became an established business coach and entrepreneur, committed to supporting others in their pursuit of personal and professional growth.
Today, Julian is a recognized corporate trainer, coach, and leader, known for his ability to leverage real-life experiences and evidence-based methodologies to affect positive change within individuals and organizations. As the leader of Zella Life's coaching division, he is dedicated to empowering individuals and businesses to achieve their full potential.